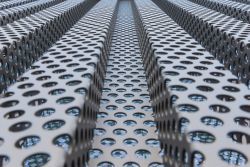
Customizing Metal Mesh: Trends in Tailored Solutions for Specific Needs
The trend toward customizing metal mesh products has gained traction across various industries, as businesses seek tailored solutions that align with their specific needs. Modern applications of custom metal mesh are particularly diverse, with manufacturers pushing the limits of what metal mesh can achieve in both functional and aesthetic terms. Here’s a closer look at how customization in metal mesh is evolving:
1. Materials and Alloys for Specialty Uses
- Range of Materials: Metals like stainless steel, aluminum, copper, brass, and bronze are popular choices due to their durability, corrosion resistance, and visual appeal. Each material offers unique advantages for different settings—stainless steel for industrial use, copper for antimicrobial applications, and aluminum for lightweight needs.
- Specialty Alloys: Unique blends, such as high-nickel alloys, are used in highly corrosive environments (e.g., chemical processing), while heat-resistant alloys cater to industries like automotive and aerospace.
2. Custom Colors and Finishes
- Anodizing and Powder Coating: These finishing techniques allow manufacturers to apply various colors to metal mesh, providing both protection and a visual appeal that complements the surroundings. Anodizing is often chosen for its durability and color retention, while powder coating offers a broader range of textures and colors.
- Patinas and Specialty Finishes: The rise in vintage and industrial aesthetics has increased demand for patinas and weathered finishes, which give metal mesh a unique aged or distressed look. Additionally, brushed and mirror-polished finishes are popular in architectural and interior design.
3. Pattern Customization for Functional and Aesthetic Purposes
- Mesh Density and Weave Styles: Metal mesh can be produced with varying degrees of density and weave style (e.g., crimped, plain, or Dutch weave) to control airflow, light diffusion, or visual privacy. This flexibility makes metal mesh ideal for filtering applications, security screens, and design partitions.
- Laser-Cut Designs: Advanced laser cutting allows intricate patterns to be cut into metal sheets, creating highly customized designs that go beyond traditional grid patterns. These unique patterns cater to decorative purposes as well as functional needs such as visibility or airflow control.
4. Innovations in Surface Treatments and Coatings
- Anti-Corrosion Coatings: In industries like marine and construction, corrosion resistance is paramount. Metal meshes can be treated with specialized coatings like zinc, epoxy, or even hybrid coatings that offer enhanced resistance to rust and degradation.
- Self-Cleaning and Hydrophobic Coatings: For architectural facades or environments prone to dust accumulation, self-cleaning coatings (e.g., titanium dioxide) are emerging as a way to reduce maintenance needs. Hydrophobic coatings are also being developed to repel water, reducing the buildup of contaminants on the mesh surface.
5. Precision Manufacturing for Specific Applications
- Architectural and Interior Design: In architecture, metal mesh is often custom-made to fit specific building requirements, with precise measurements, unique aesthetics, and compatibility with structural elements. It can serve as a façade material, interior wall cladding, or decorative ceiling.
- Automotive and Aerospace: The push for lightweight yet strong materials has led to highly specialized metal meshes that meet strict safety and performance standards. These meshes are often customized in terms of thickness, density, and pattern to optimize strength without adding unnecessary weight.
6. Sustainability and Recyclable Solutions
- Recyclable Materials: Many customized metal meshes are designed to be fully recyclable, contributing to a circular economy. Stainless steel and aluminum, in particular, are easy to recycle and retain high scrap value, making them attractive for companies prioritizing sustainability.
- Energy-Efficient Production: Environmentally-conscious manufacturers are also investing in energy-efficient production processes, and some even offer meshes made from recycled metals, aligning with growing demand for eco-friendly solutions.
7. Applications Across Industries
- Filtration and Screening: Custom mesh patterns and materials can precisely control particle size, fluid flow, and temperature resistance in filtration systems. Industries like food and beverage, pharmaceuticals, and wastewater treatment benefit from such tailored solutions.
- Security and Safety Solutions: In security applications, such as fencing and enclosures, custom metal mesh is designed with high tensile strength and unique patterns that resist cutting and other forms of tampering.
- Signage and Branding: Companies are increasingly using custom metal mesh for branding, with laser-cut logos and branded patterns for exterior signs, decorative walls, and even storefront displays.
8. Digital Design and CAD Customization
- Precision CAD Modeling: Many manufacturers offer digital design services, allowing clients to visualize and adjust their metal mesh designs before production. CAD technology enables precise customization in shape, size, and pattern density, ensuring that the final product aligns with the intended use.
- Rapid Prototyping: By using 3D printing for molds or prototyping, manufacturers can produce sample designs quickly. This technology supports quick turnarounds for custom orders and allows clients to assess the mesh before full-scale production.
Key Takeaway
The customization of metal mesh products has evolved to become highly sophisticated, enabling industries to select specific colors, patterns, materials, and finishes that meet both practical and aesthetic requirements. Whether in architecture, industrial filtration, or decorative art, tailored metal mesh solutions are more achievable and versatile than ever, supporting a wide range of unique and demanding applications.