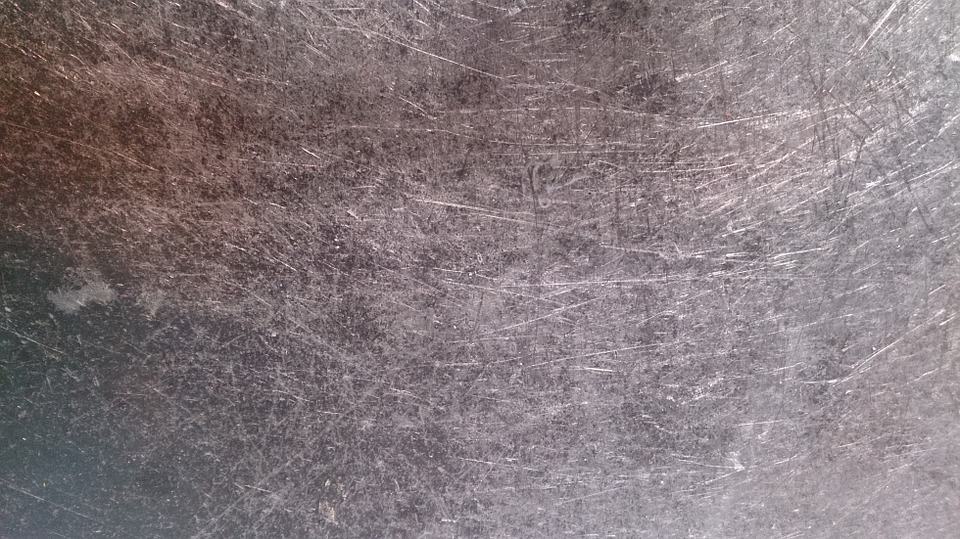
Ferritic Steel
Ferritic stainless steels are known for having good ductility, high resistance to corrosion and stress cracking, which makes them useful for applications such as automotive parts, white goods and industrial equipment.
They're available in the following grades:
- 1.4003
- 1.4016
- 1.4509
- 1.4510
- 1.4512
- 1.4521
Grade 1.4016 is the most popular grade of stainless steel; it has a medium chromium content of 16%, which corresponds to the industry standard of AISI 430. It has a higher resistance to atmospheric corrosion, which is why it is used for such a wide range of applications.
It’s resistant to most domestic liquids such as detergents, soaps and organic acids that are found in foods, which is why it is commonly used for indoor applications including washing machine drums, dishwashers, sinks, countertops and range hoods.
When the steel is used in environments that have a highly corrosive atmosphere, it becomes important to coat the steel with a smooth surface finish to avoid the material becoming stained and needing regular cleaning.
Like most ferritic stainless steels, 4016 is not susceptible to chloride-induced stress corrosion cracking and shows good resistance against many alkaline solutions and diluted organic acids, as well as liquids that do not contain halides i.e. free from chlorides, fluorides, bromides and iodides.
When the steel is exposed to elevated temperatures, it forms an oxide scale that adheres well, even during thermal cycling. For levels of constant service the upper temperature limit is 800°C in dry air.
It has good ductility and formability, but due to its lower work hardening rate, it is less suitable for applications involving stretch forming. For that same reason, it is easily cold formed and machined.
When welding 4016 it will cause some amount of martensite to form on the HAZ (heat affected zone), which is due to the higher carbon content and the lack of stabilising elements. This makes the steel is vulnerable to over-sensitisation.
A post-weld heat treatment is often required with this grade of steel; heating the steel to about 750-800°C will allow for adequate ductility and corrosion resistance to the welded area.