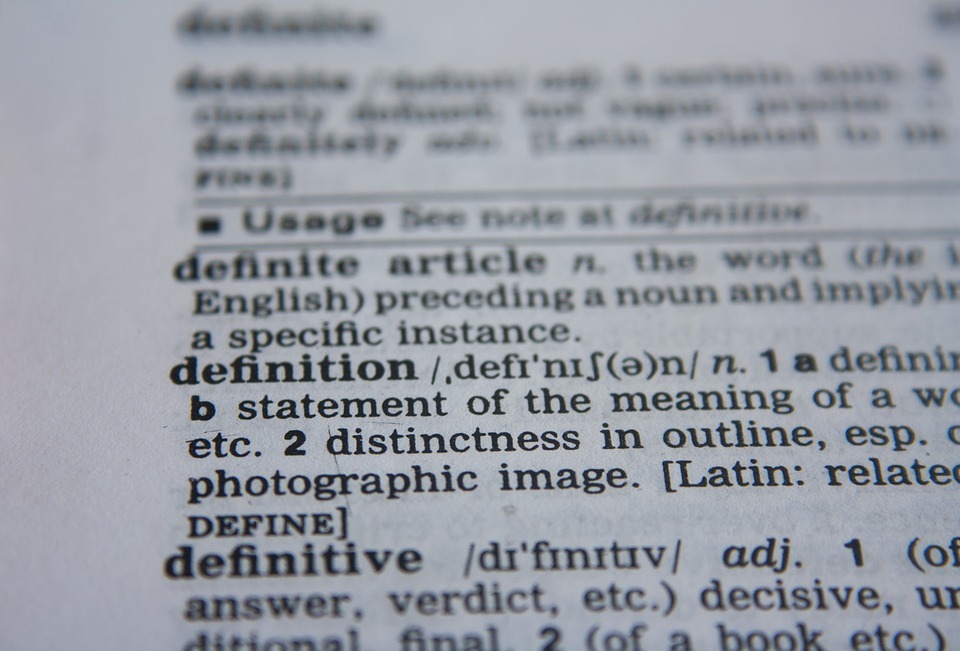
Glossary of Key Terms
Aperture: the measured open area between wires.
Backing Cloth/ Backing Mesh: wire mesh or wirecloth that is used to provide support for a screen surface.
Bolting Cloth: a group of industrial wirecloth specifications, which have a wire diameter that is lighter than the standard commercial grades to produce a larger open cloth for filtration.
Bubble Point Test: a method of testing the micron rating for dutch weaves. Measures the pressure required to pass air bubbles through the mesh. The average aperture size is then calculated by taking into consideration: surface tension, liquid density, temperature and immersion depth.
Calendering Wirecloth: process of pushing wirecloth through a set of heavy-duty rollers to either: lock the weave, flatten the wires at the knuckled (crimp) to provide a smooth surface or to reduce the thickness of the cloth (calliper).
Clear Opening: measurement of the open area between adjacent parallel wires.
Commercial Quality: wirecloth that has been manufactured for general industrial applications (see also test sieve quality).
Crimp: the dents formed in the wire during or before the weaving process to provide a locking mechanism between the warp and weft wires.
Ductility: the ability of a metal to deform plastically without fracturing
Duplex weave: like a dutch weave, but with two warp wires placed next to each other (see also dutch weave)
Dutch weave: warp wires are larger than the weft wires and spaced evenly, whilst weft wires are woven tightly together to produce a dense, strong material (see also warp and weft wires).
Elongation: the calculated percentage that a wire will stretch before it breaks.
Ferrous Alloys: alloys or materials containing iron.
Filters & Filtration: a process and device used to separate particles from liquid or gas for clarification purposes.
Filter Cake: solids retained on the filter surface during filtration.
Galvanise: the process of coating iron or steel with zinc (usually to prevent rust).
Gauge: the measured size or thickness of wire diameter.
Herringbone Twill: also known as a broken twill weave creates a distinctive V-shape weave, resembling a zig-zag, chevron pattern in the cloth. It’s created by intermittingly reserving the direction of the weave to stablish the mesh.
Hi-Flo: a plain dutch weave containing weft wires that are thinner than usual, producing a higher flow rate.
Intermediate Crimp: mesh that has extra crimps in the intersecting wires and shaped before weaving.
Mechanical Properties: refers to the physical characteristics of the wire such as tensile strength and elongation. Can also refer to the strength of woven mesh with the use of specialist equipment (see also physical properties).
Mesh Count: refers to the number of openings/apertures per linear inch.
Micron: a unit of length equal to one millionth of a metre, or a thousandth of a millimetre, 1micron=0.001mm
Multi-Ply: also known as multi-plex, it’s a weave that contains wire strands that (usually the warp wire). It is a weave that contains doubled-up wire strands (usually the warp), which are either twisted together or lye side by side. Also known as Multi-Plex.
Non-Ferrous: refers to metals or alloys that contain no iron e.g. copper, brass, aluminium
Open Area: the percentage ratio of ‘the free area between wires’ to ‘the total surface area’.
Opening: also known as aperture, it is the measured free space between two parallel wires.
Particle Retention: the size of the particle that is retained by a mesh (usually expressed in microns).
Physical Properties: refers to the physics of the metal, which do not fall under mechanical properties e.g. density, electrical conductivity, heat conductivity, thermal expansion.
Pitch: the measured distance between two parallel wires.
Plain Weave: a simple weave whereby the weft wire passes over the warp wire once, then under once and so on.
Porosity: a calculated fraction of the ‘empty’ space/ void volume of the mesh.
Raw Edge: the edge of a cut panel that has not yet been treated or tampered.
Rectangular Mesh: mesh that has a different mesh count in the warp and weft direction, resulting in a rectangular opening. The weft wire is usually heavier to stabilize the weave and has a lower mesh count than the warp wire. It can provide a larger open area than a corresponding square weave with the same micron rating (see also square mesh).
Seam: a method of joining two meshes to form a larger material
Selvage/Selvedge: refers to the edge of a wirecloth, which has been finished so that it does not unravel. Traditionally a loop edge finish.
Square Mesh: a mesh that has the same mesh count and wire diameter in both directions.
Stroke Back Edge: an edge that has been finished by brushing the wires back to form a dense layer and lock in the edge warp wire.
Tensile Strength: the maximum stress that a material can withstand while being stretched without breaking.
Test Sieve Quality: wirecloth produced in small quantities under stringent conditions to produce exact apertures (see also commercial quality).
Twill Weave: a weave whereby the weft wires pass over two warp wires, then under two, and so on.
Warp Wires: the vertical wires in a weave (see also weft wires).
Warp Beam: a beam that holds the warp wires prior to and during the weaving process.
Web: a single weaving batch.
Weft: the horizontal wires in a weave (see also warp wires).
Wirecloth: the material that is produced from weaving metal wires.
Yield Strength: the stress at which a material is transformed from an elastic state to an inelastic state.
See also our ABBREVIATIONS explained page for more jargon-busting definitions