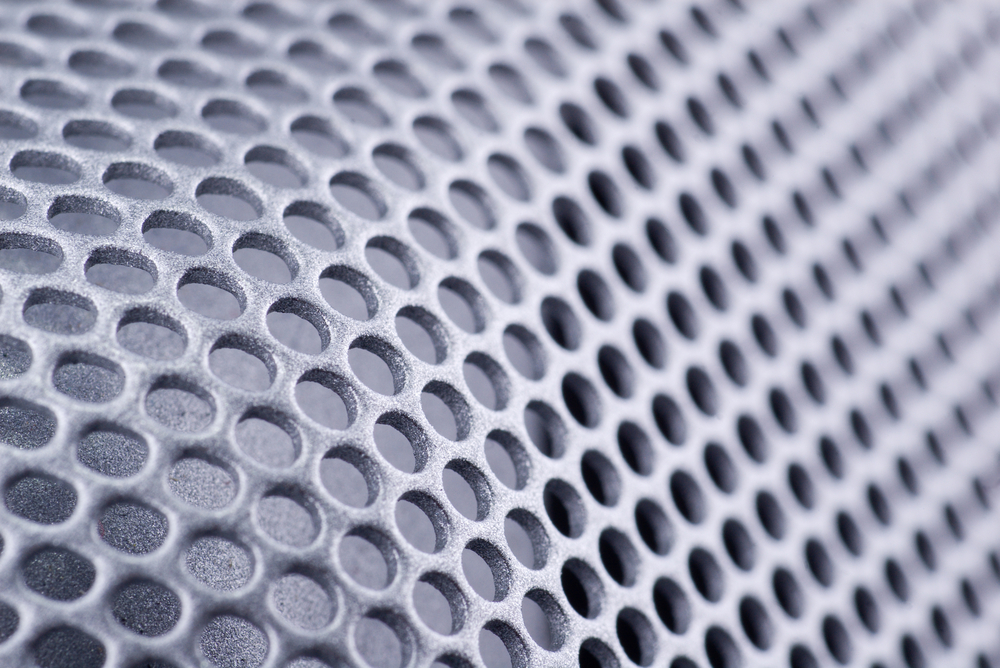
Perforated sheets in Automotive: Lightweight and High Strength Solutions
Perforated sheets play a crucial role in automotive applications, offering lightweight and high-strength solutions for various components. Here are some ways perforated sheets are used in the automotive industry:
- Noise Reduction and Vibration Damping: Perforated sheets are used as sound absorbers and vibration dampers in vehicles. They are often installed in the engine compartment, wheel wells, and undercarriage to reduce noise and vibration, providing a quieter and more comfortable ride for passengers.
- Airflow Management: Perforated sheets are used in air intake and exhaust systems to regulate airflow and improve engine performance. They are also used in the design of air vents and grilles to provide adequate ventilation while maintaining a sleek and stylish appearance.
- Structural Components: Perforated sheets are used in the construction of lightweight and high-strength structural components such as body panels, chassis, and frames. Their unique perforation patterns and material properties allow for optimal strength-to-weight ratios, making them ideal for applications where weight reduction is critical.
- Heat Dissipation: Perforated sheets are used in the design of heat shields and thermal barriers to dissipate heat generated by the engine, exhaust system, and other components. They are also used in the construction of radiators and heat exchangers to improve cooling efficiency.
- Aesthetic Design: Perforated sheets are often used in the design of decorative trim, grilles, and body panels to enhance the aesthetic appeal of vehicles. They can be customized with various perforation patterns and finishes to achieve the desired look and feel.
Overall, perforated sheets offer a versatile and cost-effective solution for a wide range of automotive applications, providing lightweight, high-strength, and aesthetically pleasing options for designers and manufacturers.