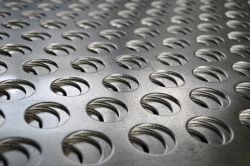
Perforated vs. Woven Metal Mesh: Which is Best for Your Project?
Compare the benefits and drawbacks of perforated and woven metal mesh to help readers choose the best option for their application.
When deciding between perforated metal mesh and woven metal mesh for a project, it's essential to evaluate their benefits and drawbacks in relation to your specific application. Here's a comprehensive comparison to help you choose the best option:
Perforated Metal Mesh
What It Is
Perforated metal mesh consists of a solid sheet of metal that has been punched or stamped with holes in a specific pattern. These holes can be round, square, slotted, or custom shapes.
Benefits
- Strength and Durability
- Maintains structural integrity because it's a single sheet of metal.
- Excellent for applications requiring load-bearing capacity, such as stairs, walkways, and railings.
- Customization
- Hole patterns, sizes, and shapes can be tailored to your project.
- Offers a sleek, modern aesthetic.
- Efficient Airflow and Light Diffusion
- Provides excellent control over ventilation and light, making it ideal for HVAC systems, facades, and sunshades.
- Ease of Cleaning
- Smooth, flat surfaces make it easy to clean and maintain.
Drawbacks
- Cost
- Generally more expensive to produce due to the manufacturing process.
- Waste material from punching out holes can add to costs.
- Limited Flexibility
- Less adaptable than woven mesh in terms of bending and shaping for complex geometries.
- Heavier
- Tends to weigh more than woven mesh for the same area due to its solid construction.
Woven Metal Mesh
What It Is
Woven metal mesh is made by interlacing metal wires in a crisscross pattern. It comes in a variety of weaves (e.g., plain, twill, Dutch) to suit different needs.
Benefits
- Flexibility
- Highly versatile and pliable, making it suitable for complex shapes and curved surfaces.
- Ideal for applications like filters, sieves, and artistic installations.
- Lightweight
- Typically lighter than perforated mesh, which can reduce material and installation costs.
- High Precision
- Offers precise openings, making it ideal for filtration and sieving applications.
- Cost-Effective
- Wires can be manufactured and woven efficiently, often resulting in lower costs compared to perforated options.
- Aesthetic Appeal
- Its textured appearance can add a unique design element to projects like facades and decorative panels.
Drawbacks
- Weaker than Perforated Mesh
- Can deform more easily under high loads or impacts.
- Not ideal for heavy-duty or load-bearing applications.
- Maintenance Challenges
- More prone to trapping dirt and debris, making cleaning difficult in some cases.
- Limited Privacy
- The open weave pattern often allows greater visibility compared to the customizable opacity of perforated mesh.
Key Considerations When Choosing
- Application Requirements
- For load-bearing and structural uses, perforated metal mesh is better due to its strength.
- For flexible, lightweight, or filtration needs, woven metal mesh excels.
- Design and Aesthetics
- Perforated mesh offers clean, modern lines, while woven mesh provides texture and intricacy.
- Cost and Budget
- Woven mesh is often the more budget-friendly option, particularly for lightweight applications.
- Environment
- If exposure to dirt or debris is a concern, perforated mesh is easier to maintain.
- Customization Needs
- For highly specific patterns or hole sizes, perforated mesh allows more control.
Summary Table
Feature | Perforated Metal Mesh | Woven Metal Mesh |
---|---|---|
Strength | High | Moderate |
Flexibility | Low | High |
Weight | Heavier | Lighter |
Customization | Extensive (hole shapes, sizes, patterns) | Limited to weave styles |
Cost | Higher | Lower |
Ease of Maintenance | Easy | Moderate to Difficult |
Aesthetic Appeal | Modern, Sleek | Textured, Intricate |
Applications | Load-bearing, facades, ventilation | Filtration, artistic, curved surfaces |
Conclusion
- Choose perforated metal mesh for structural strength, modern aesthetics, and ease of maintenance.
- Opt for woven metal mesh for flexibility, cost-efficiency, and lightweight or filtration-focused applications.
By aligning the strengths of each type with your project's priorities, you can ensure the best results.