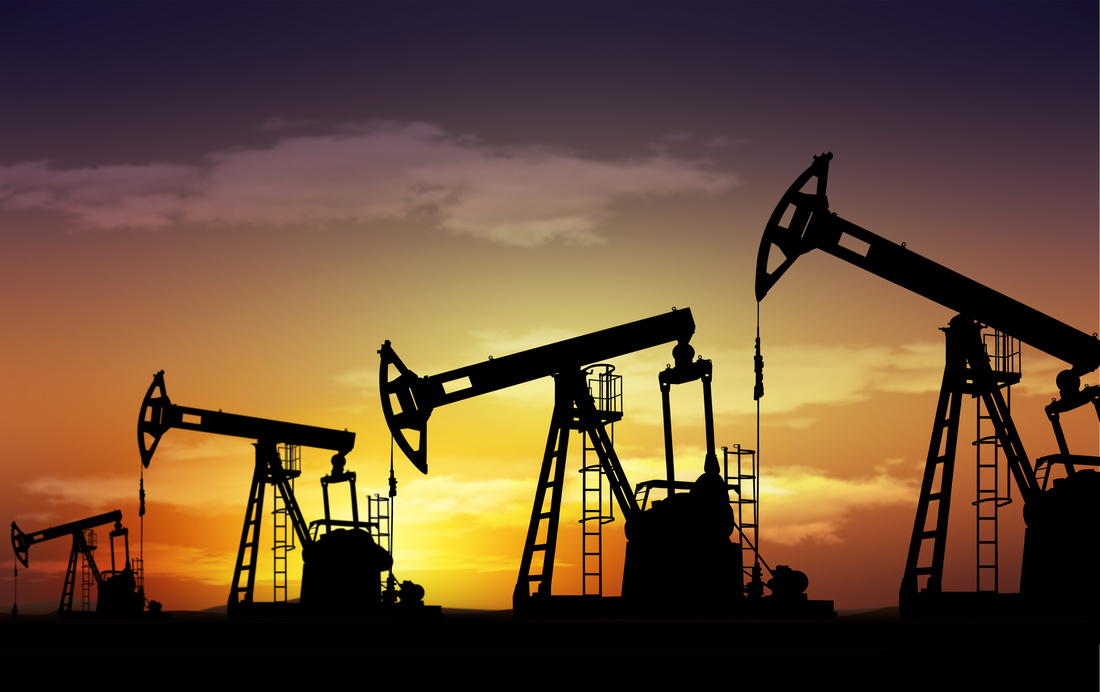
User Innovations in perforated sheet manufacturing: A look at the Latest Technologies
Perforated sheet manufacturing has seen significant advancements in recent years, driven by technological innovations aimed at improving efficiency, precision, and versatility. Here are some of the latest technologies shaping the industry:
- Laser Cutting: Laser technology has revolutionized perforated sheet manufacturing by offering precise and clean cuts on various materials, including metals, plastics, and composites. Laser cutting allows for intricate designs, tight tolerances, and high-speed production, making it ideal for custom perforation patterns and complex geometries.
- CNC Punching: Computer Numerical Control (CNC) punching machines have become increasingly sophisticated, enabling manufacturers to produce perforated sheets with greater accuracy and efficiency. These machines use programmed commands to punch holes of different shapes and sizes into sheet materials, offering flexibility for diverse applications.
- Automated Perforation Systems: Automated perforation systems integrate advanced robotics, sensors, and computer vision technology to streamline the perforation process. These systems can automatically adjust parameters such as hole size, pattern, and spacing, reducing manual intervention and minimizing errors.
- Microperforation Technology: Microperforation involves creating extremely small holes in materials, typically for applications such as filtration, acoustic panels, or decorative purposes. Advanced microperforation techniques utilize specialized tools and control systems to achieve precise perforation sizes and patterns on thin materials.
- 3D Printing/Additive Manufacturing: Additive manufacturing techniques, such as 3D printing, are being explored for perforated sheet production, particularly for prototyping and low-volume manufacturing. These technologies offer design flexibility and can produce complex perforation patterns directly from digital models, reducing the need for traditional tooling.
- Inline Inspection and Quality Control: Innovations in inline inspection systems allow manufacturers to monitor perforated sheet production in real-time, ensuring consistent quality and detecting defects promptly. These systems employ sensors, cameras, and data analytics to analyze perforation accuracy, surface finish, and other critical parameters.
- Environmentally Friendly Processes: With increasing emphasis on sustainability, manufacturers are developing eco-friendly perforation techniques that minimize waste, energy consumption, and environmental impact. This includes optimizing manufacturing processes, recycling scrap materials, and using environmentally friendly coatings or treatments.
- Collaborative Robotics (Cobots): Collaborative robots, or cobots, are being integrated into perforated sheet manufacturing facilities to assist workers in tasks such as material handling, loading/unloading, and quality inspection. Cobots can improve productivity, ergonomics, and safety while working alongside human operators.
Overall, these advancements in perforated sheet manufacturing technologies are driving innovation across various industries, enabling the production of high-quality perforated products with enhanced functionality and performance. As technology continues to evolve, we can expect further improvements in efficiency, customization, and sustainability within the perforated sheet manufacturing sector.